Автоматическая сварка тавровых и нахлёсточных соединений под флюсом
Автоматическая сварка тавровых и нахлёсточных соединений, в зависимости от
конструктивных особенностей свариваемых изделий, осуществляется вертикальным
электродом, при положении сварного соединения “в лодочку” (схема а)
на рисунке ниже), или наклонным электродом в том случае, когда один из листов
или оба листа имеют горизонтальное положение (схема б) на рисунке ниже:
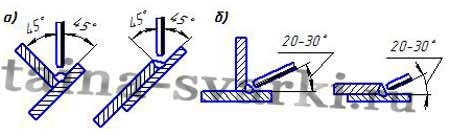
При этом сварка может выполняться с односторонней разделкой кромок, с двухсторонней,
или, вообще без разделки и зависит это от толщины свариваемого металла (см.
рисунок ниже), а также от требований, предъявляемых к металлоконструкции и условий
её эксплуатации.
Если зазор между свариваемыми деталями не превышает 1мм, сварка в “лодочку”
осуществляется на весу и дополнительные приспособления (металлические подкладки
и флюсовую подушку) не используют. При большом зазоре, превышающем 1мм, применяют
сварку на медных или стальных подкладках, или на флюсовой подушке. Возможна
заделка зазора асбестовыми уплотнениями, или выполнение подварочного шва с обратной
стороны.
Сварка “в лодочку” позволяет равномерно проварить кромки свариваемого
изделия и получить качественный сварной шов большого сечения за один проход.
Но для того, чтобы осуществить такую сварку, необходимы специальные кантователи,
на которые устанавливают сварное соединение.
При автоматической сварке под флюсом тавровых или нахлёсточных соединений наклонным
электродом, он находится под углом 20-30° к горизонту. Такой способ сварки не
позволяет получить сварные швы с катетом более 16мм, что является его недостатком.
Поэтому часто приходится применять многослойную сварку. Приблизительные режимы
автоматической сварки тавровых и нахлёсточных соединений “в лодочку”,
выполняемой сварочной проволокой диаметром 5мм, можно выбрать по таблице:
Катет шва, мм | Сила тока, А | Напряжение дуги, В | Скорость сварки, м/ч | Скорость подачи проволоки, м/ч |
5 | 600-650 | 34-36 | 58,0 | 60,7 |
6 | 650-700 | 34-36 | 47,0 | 67,3 |
7 | 700-730 | 34-36 | 38,5 | 71,1 |
8 | 700-750 | 34-36 | 32,0 | 73,5 |
9 | 750-780 | 34-36 | 27,5 | 78,0 |
10 | 750-800 | 34-36 | 24,0 | 81,3 |
12 | 850-900 | 34-36 | 19,0 | 95,3 |
14 | 900-950 | 36-38 | 16,0 | 103,0 |
16 | 950-1000 | 38-40 | 13,0 | 111,0 |
Дополнительную информацию о выборе режимов сварки, в зависимости от свариваемого
материала и его толщины, можно узнать на странице: “Режимы
для автоматической сварки под флюсом”.
Дополнительные материалы по теме:
Плавленые | Технология |
Виды применяемых флюсов
Перед тем, как провести сварку под флюсом, неплохо было бы узнать, какие вообще бывать разновидности. Прежде всего, всю флюсы делятся по назначению. Они могут быть для сварки углеродистых и легированных сталей, для высоколегированных сталей и для цветных металлов
Это первое, на что стоит обратить внимание перед покупкой флюса
Также флюсы могут быть плавлеными или керамическими. Их отличие в составе. В большинстве случаев используется именно плавленый флюс, поскольку он относительно универсальный и стоит недорого. С его помощью можно эффективно защитить сварочную ванну от кислорода. Но не ждите от плавленого флюса каких-то особых качеств. Если вам необходимы действительно отличные свойства шва, то выберите керамический флюс. Он обеспечивает отличное качество.
Также флюсы могут быть химически активными и химически пассивными. Активный флюс содержит в составе кислоты, способные не только защитить металл при сварке, но и привести к коррозии. Так что тщательно удаляйте флюс после работы. Пассивные флюсы в автоматической сварке не применяются, поскольку не обладают достаточными для этого свойствами. Зачастую вы встретите пассивный вещества при пайке в виде воска или канифоли.
Кстати, о производителях. Это давний спор всех начинающих и опытных сварщиков. Кто-то считает, что отечественные компании производят недорогой и эффективный флюс, а кто-то всеми руками за импортные комплектующие. Мы не будем однозначно говорить, что лучше, скажем лишь то, что на практике и отечественные, и импортные флюсы показывают себя хорошо, если соблюдена технология сварки.
Виды флюсов
Как уже было сказано выше, флюс для сварки – это порошок с размерами гранул 0,2-4 мм. Его классификация зависит от многих показателей. Но есть основные характеристики, которые разделяют его на группы и классы.
По способу производства сварочные флюсы делятся на:
- плавленые: их компоненты сначала плавятся, затем гранулируются, прокаливаются и разделяются на фракции;
- неплавленые или керамические: это сухие ингредиенты, которые смешиваются с жидким стеклом, сушатся, гранулируются, прокаливаются и разделяются на фракции.
Производители и специалисты отмечают плавленый вариант, как лучший из двух представленных.
Разделение по химическому составу.
- Оксидные флюсы. В основе порошка содержатся оксиды металлов до 90% и остальное – это фторидные соединения. В этой группе есть подгруппы, которые определяют процентное содержание того или иного оксида. К примеру, оксид кремния. Если его содержится во флюсе до 1%, то такой порошок называется бескремнистый, если его содержание составляет 6-35% – низкокремнистый и больше 35% – высококремнистый. Оксидные флюсы предназначены для сварки низкоуглеродных и фтористых стальных заготовок.
- Солевые. В них нет оксидов металлов, основу составляют соли: фториды и хлориды. Такой порошок используется для сваривания активных металлов, к примеру, титан.
- Смешанные флюсы (солеоксидные). В них есть и оксиды и соли. Применяют их для соединения легированных сплавов.
Еще одна характеристика – активность флюсов. По сути, это скорость окисления порошка при его нагреве. Измеряется данный показатель от нуля до единицы и делит флюсы на четыре категории:
- Меньше 0,1 – это пассивные материалы.
- От 0,1 до 0,3 – малоактивные.
- От 0,3 до 0,6 – активные.
- Выше 0,6 – высокоактивные.
И последнее. Это деление по строению гранул. Здесь три позиции: стекловидные, пемзовидные и цементированные. Необходимо отметить, что сварка под стекловидным флюсом дает более широкий сварной шов, чем под пемзовидным. Если используется порошок с мелкими частицами, то шов под ним образуется глубокий и неширокий с высокими прочностными качествами.
Головной Аттестационный Центр «Мосты»
При изготовлении и монтаже сварных мостовых металлоконструкций надлежит применять преимущественно электродуговую автоматическую и механизированную сварку под флюсом и в смеси защитных газов. Допускается применение ручной дуговой сварки. Области применения разрешенных способов сварки для мостовых конструкций приведены ниже в таблицах 1 и 2. Способ сварки должен быть указан на чертежах КМ, КМД и в технологической документации. Таблица 1 — Заводское изготовление мостовых металлоконструкций (КСМ, п.1)
№ | Наименование способа сварки и область применения |
1 | Ручная дуговая сварка (РД): — стыковые и угловые соединения толщиной 10-50мм во всех пространственных положениях. — исправление дефектов после автоматической или механизированной сварки. |
2 | Механизированная сварка под флюсом (МФ): — стыковые соединения толщиной 10-25мм в нижнем положении. — угловые соединения толщиной 10-50мм в нижнем положении. |
3 | Механизированная сварка в смеси защитных газов (МП, МПГ, МПС): — стыковые соединения толщиной 6-25мм в нижнем положении. — угловые соединения толщиной 10-50мм во всех пространственных положениях. |
4 | Автоматическая сварка под флюсом (АФ): — стыковые соединения толщиной 10-50мм в нижнем положении двусторонней сваркой на флюсовой подушке. — стыковые соединения толщиной 10-20мм включительно в вертикальном положении односторонней сваркой. — угловые соединения толщиной 10-50мм в нижнем положении односторонней и двусторонней сваркой. |
5 | Автоматическая сварка в смеси защитных газов (АПГ, АППГ): — стыковые соединения толщиной 6-25мм в нижнем положении. — угловые соединения толщиной 10-50мм в во всех пространственных положениях. |
6 | Автоматическая сварка самозащитной проволокой (АПС): — стыковые соединения толщиной 10-40мм включительно в вертикальном положении. |
7 | Контактно-стыковая сварка оплавление (КСО): — сварные соединения гибких упоров в виде круглых стержней диаметрами 19мм, 22мм, 25мм с головкой. |
Таблица 2 — Монтажная сварка мостовых металлоконструкций (КСМ, п.2)
№ | Наименование способа сварки и область применения |
1 | Ручная дуговая сварка (РД): — стыковые и угловые соединения толщиной 10-50мм во всех пространственных положениях. — исправление дефектов после автоматической или механизированной сварки. — подварка корня сварного стыкового шва под автоматическую или механизированную сварку. |
2 | Механизированная сварка под флюсом (МФ): — стыковые соединения толщиной 10-25мм в нижнем положении. — угловые соединения толщиной 10-50мм в нижнем положении. |
3 | Механизированная сварка в смеси защитных газов (МП, МПГ, МПС): — стыковые соединения толщиной 6-25мм во всех пространственных положениях. — угловые соединения толщиной 10-50мм во всех пространственных положениях. — подварка корня сварного стыкового шва под автоматическую сварку. |
4 | Автоматическая сварка под флюсом (АФ): — стыковые соединения толщиной 12-50мм в нижнем положении односторонней сваркой с МХП. — стыковые соединения толщиной 10-20мм включительно в вертикальном положении односторонней сваркой. |
5 | Автоматическая сварка под флюсом с МХП по ручной подварке корня шва (РД+АФ): — стыковые соединения толщиной 12-50мм в нижнем положении односторонней сваркой по ручной подварке корня шва. — стыковые соединения двухлистовых пакетов толщиной 40-100мм в нижнем положении односторонней сваркой в комбинации с ручной сваркой. |
6 | Автоматическая сварка в смеси защитных газов (АППГ): — стыковые соединения толщиной 10-40мм включительно в вертикальном положении. |
7 | Автоматическая сварка самозащитной проволокой (АПС): — стыковые соединения толщиной 10-40мм включительно в вертикальном положении. |
8 | Контактно-стыковая сварка оплавление (КСО): — сварные соединения гибких упоров в виде круглых стержней диаметрами 19мм, 22мм, 25мм с головкой. |
Полезные советы
- Большое значение в технологии сварки под флюсом играет переход металлов (марганца и кремния) в металл сварочного шва. Марганец переходит быстрее, если концентрация его оксида (MnO) больше, чем оксида кремния (SiO2). Чем меньше активность флюса, тем быстрее происходит переход.
- Поры в швах образуются, если флюс не был хорошо просушен, если он не соответствует свойствам металла свариваемых заготовок и металлу присадочной проволоки, если между деталями оказался слишком большой зазор, если флюсовый слой оказался недостаточным, если его качества низкие.
- Негативно на сварочный шов влияет водород. Поэтому его с помощью флюсов связывают в нерастворимые соединения. Это лучше делает порошок с большим содержанием кремния и с пемзовидной формой гранул.
- Чтобы в сварном шве не образовывались трещины, необходимы флюсы с высоким содержанием и кремния, и марганца.
Сегодня все чаще в промышленности используется сдвоенная или двухэлектродная сварка, в которой электроды располагаются на расстояние меньше 20 мм друг от друга и питаются от одного источника электрической энергии. При этом они варят в одной зоне, формируя единую сварочную ванну. Располагаться электроды могут как в продольном положении, так и в поперечном.
Применяют и двухдуговую сварку, в которой расходники питаются от двух разных источников, при этом ток может быть на двух стержнях переменным или постоянным. А может быть и разным. Расположение же электродов может быть перпендикулярным плоскости сваривания или под наклоном. Варьируя углом наклона, можно увеличить глубину проварки или уменьшить. Соответственно будет изменяться и ширина шва.
Дуговая сварка под флюсом может проводиться и при повышении расстояния между расходниками. В этом случаи сварка будет проводиться параллельно в двух ваннах. Но первый электрод будет выполнять функции нагревателя зоны сварки, второй будет ее проваривать. При такой технологии соединения металлических заготовок электроды устанавливаются перпендикулярно плоскости сваривания. Данный способ отличается тем, что в процессе сварки двумя электродами не образуются закалочные участки как в самом сварочном шве, так и в прилегающих к нему зонах на основных деталях.
Технология сварки под флюсом
Сварка под флюсом ГОСТ 8713-79 выполняется тремя способами:
Автоматическим;
Полуавтоматическим;
Ручным способом.
Автоматическая сварка под слоем флюса выполняется сварочными машинами. Все режимы выставляются на машине и не требует участия человека. Соединение получается качественным, без дефектов.
Сварочные автоматы под слоем флюса бывают трёх типов:
1.Тракторы;
2.Подвесные;
3.Многодуговые.
К аппаратам тракторного типа можно отнести автоматы А-1506 и А-1648 и подвесные аппараты А-1400. К многодуговым относятся универсальные аппараты, которые могут перемешаться по поверхности, как трактор, так и быть подвесными. Такими аппаратами являются А-1412 и ДТС-38.
Обычно, сварка трактором под флюсом применяется для деталей с ровной поверхностью и длинной протяжённостью.
При полуавтоматической сварки под флюсом, происходящий процесс контролирует сварщик. Такой способ похож на полуавтоматическую сварку в среде защитного газа СО2.
Ручная сварка под флюсом осуществляется неплавящимся электродом с подачей в него флюса. Сварщик самостоятельно «дозирует» количество поступаемого флюса в зону сварки нажатием на кнопку.
Режимы сварки под слоем флюса
Все режимы сварки под слоем флюса выбираются от диаметра проволоки. Диаметр проволоки выбирается в зависимости от толщины листа. При толщине металла от 5 до 8 мм выбирается проволока Ø 2 – 3 мм. Если толщина металла составляет 10 — 20 мм, тогда следует применять проволоку Ø 4 – 5 мм.
В связи с тем, что каждый сварочный аппарат имеет свои индивидуальные характеристики, при выборе режимов сварки, необходимо руководствоваться рекомендациям в паспорте к установке.
Ниже приведены приблизительные режимы для сварки под слоем флюса:
Металл | Толщина металла, мм | Форма кромок | Зазор, мм | Диаметр проволоки, мм | Сварочный ток, А | Напряжение, В | Скорость сварки, м/ч |
Стали: Низкоуглеродистые, среднеуглеродистые, высокоуглеродистые | 3 | Без разделки | 0-1 | 2 | 250-500 | 28-30 | 48-50 |
5 | Без разделки | 0-2 | 2 | 400-450 | 28-30 | 38-40 | |
10 | Без разделки | 2-4 | 5 | 700-750 | 34-38 | 28-30 | |
20 | Без разделки | 2-4 | 5 | 750-800 | 38-42 | 22-24 | |
30 | Без разделки | 4-6 | 5 | 950-1000 | 40-44 | 16-18 | |
6 | V — разделка | 3 | 250-280 | 28-32 | 25-28 | ||
10 | V — разделка | 3 | 350-380 | 32-36 | 17-20 | ||
12 | V — разделка | 5 | 500-550 | 36-40 | 30-36 |
Подготовка к сварке
Прежде чем приступить к работе, необходимо:
1. Выложить свариваемые детали на стенд. Выставить необходимый зазор и прижать их при необходимости струбцинами к сварочному столу.
2. Зачистить поверхность металла от грязи и ржавчины.
3. Засыпать в бункер аппарата флюс.
4. Установит бухту с проволокой.
5. Задать сварочному аппарату необходимые режимы сварки.
6. Выполнить заварку металла.
Преимущества и недостатки
Основные преимущества сварки под флюсом:
За счёт использования автоматических аппаратов, можно добиться качественного сварного соединения. За счёт автоматики, есть возможность выставления скорости сварки, подачи проволоки, сварочного тока и зазора между проволокой и изделием.
Беспрерывная подача флюса защищает расплавленную ванну от вредных воздействий из вне. Дополнительно флюс легирует сварной шов, увеличивая его прочностные качества.
Основные недостатки сварки под флюсом:
Сложность настройки такого оборудования. У сварщика нет возможности проконтролировать процесс сварки, так как шов спрятан за слоем флюса.
Нет возможности варить изделия в вертикальном и потолочном положении. При больших неровностях изделия, сварка может быть невозможна.
Оборудование, которым осуществляют сварку под флюсом
Рассмотрим существующее оборудование для сварки под флюсом. Когда речь идет о проведении сварочных работ в условиях производственного цеха, то перед началом процесса сварки свариваемые детали надежно фиксируют на специальном сборочном стенде или при помощи других приспособлений, чтобы полностью исключить возможные незапланированные движения свариваемых элементов в ходе работы.
Сварочный трактор (производитель Multitrac)
На прокладке трубопроводов для сваривания стыков в основном используют специальные мобильные сварочные головки, а при производстве листовых конструкций применяются либо стационарные установки, либо универсальные мобильные (к примеру, сварочный трактор). Трактор для сварки под слоем флюса – это самоходная тележка с электродвигателем, на которой установлена автоматическая сварочная головка. Такое устройство может двигаться вдоль свариваемых деталей по рельсовому пути или же непостредственно по самим деталям.
Сварочная колонна и свариваемая деталь на роликовых опорах
В условиях цехов также активно используются передвижные или стационарные сварочные колонны, которые в комбинации с роликовыми опорами или вращателями служат для сварки продольных и кольцевых швов.
Это интересно: Сварка титана и его сплавов — технология и особенности
3 Какие материалы используют для сварочных работ под флюсом?
От грамотного подбора электродной проволоки зависит качество сварки. Ее химсостав устанавливает механические параметры шва. Рекомендуется применять стальную проволоку, которая соответствует Государственному стандарту 2246-70. Изготавливают ее из легированной, низкоуглеродистой и высоколегированной стали. Диаметры готовой проволоки при этом стандартизированы, они варьируются в пределах от 0,3 до 12 мм.
Поставляется такая продукция обычно в 80-метровых (не более) бухтах, реже в кассетах либо катушках (требуется согласие потребителя). Перед использованием проволоки, хранившейся некоторое время на складах, профессионалы советуют производить ее очистку и специальную несложную обработку бензином или керосином, что позволяет удалить ржавчину и загрязнения с изделия.
Для сварки изделий из алюминиевых листов выпускают проволоку по стандарту 7871-75. Также часто применяют омедненную проволоку (ГОСТ 16130-72), которая не требует предварительной обработки перед сваркой. На условия протекания сварочного процесса и качество шва, конечно же, оказывает влияние и то, какой флюс был выбран. Его состав определяет характеристики газовой атмосферы и жидкого шлака. От взаимодействия последнего с металлом в свою очередь зависит и структура металла шва. А она обуславливает стойкость против формирования трещин.
Выбирая флюсы, стоит помнить, что они необходимы для:
- легирования металла шва;
- изоляции (физического плана) сварочной ванны от окружающей среды;
- создания поверхности шва;
- стабилизации разряда дуги.
Сущность процесса сварки под флюсом
Схемы сварки
На рисунке схематично показан процесс сварки под слоем флюса. Между свариваемым
изделием (поз.1) и концом сварочной проволоки (поз.3) горит сварочная дуга (поз.4),
под воздействием которой проволока расплавляется и подаётся в зону сварки. Слой
сварочного флюса (поз.2) закрывает дугу.
Сварочная проволока вместе с дугой перемещается вдоль свариваемого стыка при
помощи механизмов или вручную. Под воздействием сварочной дуги происходит расплавление
основного металла и флюса. Получившийся расплав образует сварочную ванну. Жидкий
флюс в виде плёнки на поверхности ванны (поз.5) изолирует зону сварки от окружающей
среды.
Расплавленный
металл переходит в сварочную ванну, где смешивается с расплавленным основным
металлом (поз.9). По мере того, как сварочная дуга отдаляется от свариваемого
участка, металл охлаждается и затвердевает, образуя сварочный шов (поз.8). Расплавленный
флюса некоторое время ещё остаётся жидким, когда металл уже затвердел. Затем
затвердевает и флюс, образуя на поверхности шва шлаковую корку (поз.6). Излишняя,
нерасплавленная часть флюса (поз.7) собирается и используется повторно.
Особенности дуговой сварки под слоем флюса
Дуговую механизированную сварку под флюсом от других способов сварки плавлением
отличает высокая производительность и лучшие гигиенические условия труда. Флюс
защищает не только сварочную ванну от воздействия окружающей среды, но и, в
свою очередь, окружающую среду от вредных воздействий и испарений различных
веществ в процессе сварки.
Кроме этого, данный вид сварки отличает высокий уровень механизации сварочных
работ. Сварочная проволока плавится под действием электрической дуги, а флюс
обеспечивает ведение процесса, требуемое качество сварки и применяется при сварке
и наплавке под флюсом, сварке по флюсу, сварке с магнитным флюсом, а также при
электрошлаковой
сварке и наплавке.
Роль флюса при сварке
Сварочный флюс обеспечивает ровное горение дуги, формирование сварного шва
и оказывает влияние на его химический состав. Также он определяет стойкость
швов к образованию холодных трещин, пор и других сварочных
дефектов.
Наличие в составе флюса оксидов щелочных и щелочноземельных металлов способствует
увеличению электропроводности и длины дугового промежутка, что делает процесс
сварки более устойчивым. Наличие фтора, наоборот, снижает эти характеристики.
Таким образом, флюсы с разными составами обладают разными стабилизирующими свойствами.
Изменяя содержание углерода, серы, марганца и других элементов, флюс оказывает
сильное влияние на стойкость швов к холодным трещинам. Увеличение содержания
серы, фосфора и углерода снижает, а увеличение содержания марганца повышает
стойкость сварных швов к образованию трещин. Кроме этого, состав от состава
флюса зависит, насколько легко будет отделяться шлаковая корка от поверхности
готового сварного шва. Этот показатель тоже важен, поскольку он влияет на производительность
процесса. Легкая отделимость шлаковой корки – это необходимое условие для высокой
производительности.
Схема процесса автоматической сварки под флюсом
На схеме показана сущность процесса автоматической сварки под флюсом. Процесс
сварки рекомендуется выполнять на специальной подкладке поз.1. Подача сварочной
проволоки в зону сварки происходит автоматически. Электрическая дуга возбуждается
автоматически между концом электрода поз.4 и свариваемым металлом поз.2 и находится
она под слоем сварочного флюса, поз.6. Подача флюса производится при помощи
бункера поз.3.
В результате теплового воздействия электрической дуги, происходит расплавление
сварочной проволоки и свариваемого металла. Также происходит расплавление флюса,
попавшего в зону сварки. В зоне действия электрической дуги формируется некоторое
пространство, ограниченное сверху плёнкой из расплавленного флюса. Это пространство
занимают пары расплавленного металла, флюса и газы, образующиеся при сварке.
Давление смеси газов и паров в этом пространстве удерживают флюсовую плёнку,
которая находится над зоной сварки. Электрическая дуга поз.5 всегда находится
рядом со сварочной ванной, вблизи от её переднего края. Дуга, из-за её постоянного
движения, горит не вертикально, а немного отклоняется в обратную сторону от
направления сварки.
Электрическая дуга воздействует на расплавленный металл и оттесняет его в сторону,
противоположную направлению сварки. В результате формируется сварочная ванна
поз.8.
Непосредственно под электродом формируется кратер, с небольшим количеством
жидкого металла. Но наибольший объём расплавленного металла располагается в
зоне от кратера до поверхности сварного шва поз.12. Расплавленный флюс поз.7
имеет значительно меньшую плотность, по сравнению с жидким металлом и всплывает
на поверхность сварочной ванны, охватывая её плотной оболочкой. Флюсовая оболочка
предотвращает разбрызгивание расплавленного металла.
У расплавленного флюса теплопроводность достаточно низкая, из-за чего, охлаждение
металла замедляется. Благодаря этому, шлаковые включения и растворённые в металле
газы, поз.9, успевают подняться на поверхность и выйти из него, пока металл
находится в жидком состоянии.
Не расплавленный флюс, оставшийся “незадействованным” в процессе
сварки, откачивают пневматическим устройством поз.10 и затем используют при
дальнейшей сварке. Расплавленный в процессе сварки металла флюс, при кристаллизации
образует плотную корку на поверхности сварного шва. После окончания сварки и
охлаждения сварного соединения, шлаковую оболочку, из затвердевшего флюса, удаляют
с поверхности сварного шва поз.12.
Схема работы установки для автоматической сварки
На
рисунке справа схематично показаны основные узлы установки для автоматической
сварки и показана последовательность их работы.
Поз.5 и поз.4 – это ведущий и нажимной ролик, соответственно. Они необходимы
для подачи электродной проволоки поз.3 в зону сварки. Из бункера поз.1 в зону
сварки подаётся гранулированный флюс в зону сварки и покрывает непроницаемым
слоем свариваемые кромки поз.7.
Через мундштук поз.6 происходит подача сварочного тока к электроду. Мундштук
располагается на расстоянии 40-60мм от конца электродной проволоки и позволяет
применять сварочные токи большой величины. Между свариваемым изделием поз.11
и сварочной проволокой горит электрическая дуга и расплавляет металл, образуя
сварочную ванну. Ванну сверху закрывает расплавленный шлак поз.9 и нерасплавленный
флюс поз.8.
По мере перемещения зоны сварки вдоль кромок, флюс, оставшийся нерасплавленным,
отсасывается вытяжным шлангом поз.2 назад в бункер. Пары и газы, выделяющиеся
в процессе сварки, создают в зоне сварки газовый пузырь, который закрыт слоем
флюса и шлака.
При температурном расширении газового пузыря его давление оттесняет расплавленный
металл в зону, противоположную от зоны сварки. Т.к. горение электрической дуги
происходит внутри газового пузыря, закрытого шлаком и флюсом, угар и разбрызгивание
металла исключаются.
По мере перемещения электрической дуги вдоль сварных кромок, жидкий металл
остывает и формируется сварной шов. Как уже было сказано выше, слой шлака имеет
более низкую температуру плавления, чем свариваемый металл и затвердевает он
значительно позже, замедляя остывание расплавленного металла. Замедленное охлаждение
сварного шва способствует выходу газов из ещё жидкого металла и шов получается
более однородным по химическому составу.
5.2. Автоматическая сварка (наплавка) под флюсом
При сварке под флюсом (рис. 5.2) дуга горит между сварочной проволокой 1 и свариваемым изделием 5 под слоем гранулированного флюса 4. Ролики 2 специального механизма падают в электродную проволоку в зону дуги 6.
Рис. 5.2. Схема автоматической сварки (наплавки) под флюсом
Сварочный ток (переменный или постоянный прямой или обратной полярности) подводится к проволоке с помощью скользящего контакта 3, а к изделию – постоянным контактом. Сварочная дуга горит в газовом пузыре, который образуется в результате плавления флюса и металла.
Кроме того, расплавленный металл защищен от внешней среды слоем расплавленного флюса 8. По мере удаления дуги от зоны сварки расплавленный флюс застывает и образует шлаковую корку 10, которая впоследствии легко отделяется от поверхности шва.
Флюс засыпается впереди дуги из бункера слоем толщиной 40–80 мм и шириной 40– 100 мм. Нерасплавленный флюс после сварки используется повторно. Расплавленные электродный и основной металлы 7 в сварочной ванне перемешиваются и при кристаллизации образуют сварной шов 9.
Преимущественное применение находит сварка проволокой (проволочным электродом). Однако в последнее время все большее распространение получает наплавка ленточными или комбинированными электродами.
К достоинствам сварки под флюсом относятся: высокая производительность процесса, благодаря использованию больших токов, глубокому проплавлению, почти полному отсутствию потерь металла на угар и разбрызгивание (не более 3%); высокое качество наплавляемой поверхности в результате хорошей защиты флюсом сварочной ванны; незначительное количество неметаллических включений в металле шва; возможность легирования наплавляемого металла через флюс; лучшее использование тепла дуги (по сравнению с ручной сваркой расход электроэнергии уменьшается на 30– 40%); лучшие условия труда сварщика и ряд других.
Вместе с тем, этот вид сварки имеет ряд недостатков: значительный нагрев изделия; повышенную текучесть расплавленных металла и флюса, что позволяет вести сварку только в нижнем положении и наплавлять детали диаметром не менее 40 мм; необходимость в отдельных случаях повторной термической обработки; невозможность непосредственного наблюдения за формированием сварочного шва.
Сварка под флюсом используется при изготовлении и ремонте конструкций и деталей ответственного назначения, которые должны быть надежными при эксплуатации в условиях низких и высоких температур.
Для рассматриваемого вида сварки и наплавки при ремонте подвижного состава наибольшее применение находят флюсы марок АН-348А, АН-348В, ОСЦ-45, АНЦ-1 и др. (ГОСТ 9087-81 ФЛЮСЫ СВАРОЧНЫЕ ПЛАВЛЕННЫЕ).
Такие флюсы рекомендуются для сварки низко- и среднеуглеродистых сталей. Для сварки и наплавки низко- и среднелегированных сталей используются флюсы АН-348А, АН-60, АН-22 и другие в сочетании с проволоками марок Св-08А, Св-08ГА и проволоками, легированными хромом, молибденом, никелем. В табл. 5.3 приведено назначение некоторых марок флюсов и проволок.
Таблица 5.3
Флюсы и проволока для автоматической сварки
Для получения при восстановлении деталей слоев с повышенными физико- механическими свойствами при наплавке под флюсом используются наплавочные проволоки, которые подразделяются на 3 группы: из углеродистой стали типа Нп-30, Нп-40, Нп-80 и других; из легированной стали Нп-30Х5, Нп-30ГСА, Нп-40ХФА и других; из высоколегированной стали, например, Нп-4Х13, Нп-45Х4В3Ф, Нп-45Х2В8Т и других.
Для повышения производительности наплавки под флюсом в качестве наплавочного материала используются сплошные или порошковые ленты толщиной 0,3–1 мм и шириной 20–100 мм.
В табл. 5.4 приведены технические характеристики некоторых марок наплавочной проволоки, рекомендуемых для восстановления деталей подвижного состава.
Технические характеристики аппаратов для автоматической сварки и наплавки под флюсом приведены в табл. 6 приложения.
Таблица 5.4
Технические характеристики наплавочной проволоки*
*ГОСТ 10543-82 Проволока стальная наплавочная